Around 3 a.m. every Tuesday and Friday morning, the editors of The Maroon finish working on the newspaper layout, send PDFs of the pages off to the printer, and head home to get some rest. Hours later, over 5,000 copies of the paper can be found across campus. In an effort to better understand what happens while we’re asleep, we decided to take a trip to Litho Type LLC—the place where it all happens.
Located about 20 miles south of campus in Lansing, IL, this commercial printer has been in business for more than 40 years and is responsible for the printing of 50–60 publication issues each week. Dan Gouwens, co-owner of the company, met with a few members of The Maroon staff last week to offer a glimpse of the printing press in action.
Currently, there are 32 employees, part and full time, working at Litho Type. The average employee has worked there for 25 years, according to Gouwens. Some employees work upstairs, taking care of the business and operations end, and others work downstairs at the printing press.
“You guys missed the fun part,” Gouwens said. “The fun part was 20 years ago when we worked with razor blades. The schools had students out here to put the pages together and proofread. They were here all night.” Before the age of desktop publishing, newspapers were produced through the process of phototypesetting, which used film negatives to project text onto photographic paper. The paper was then developed in a chemical bath and cut and arranged manually to create the page layout.
The technology that Litho Type now uses to print the newspaper is much more advanced and streamlined. Practically every step of the process is automated, with a variety of machines working in unison to turn an electronic copy of a page into the real thing. The printing press is constantly in motion, emanating a loud humming noise as it churns out page after page. Gouwens said the process generates very little waste, as nearly everything (newsprint, chemicals, scrap metal, etc.) is recycled after the printing process is complete.
Gouwens believes that, despite the move to online news websites, a news publication could not exist without its print counterpart. “You still need a hard copy if you’re going to have a publication. I don’t think you can just do an online copy. But what do I know? I’m a printer,” he laughed.
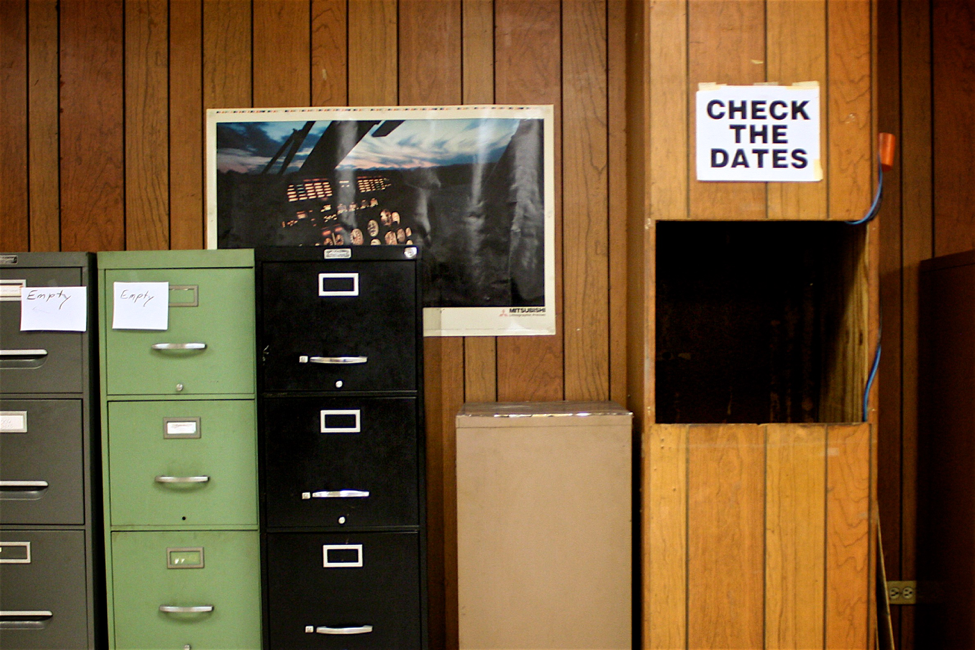
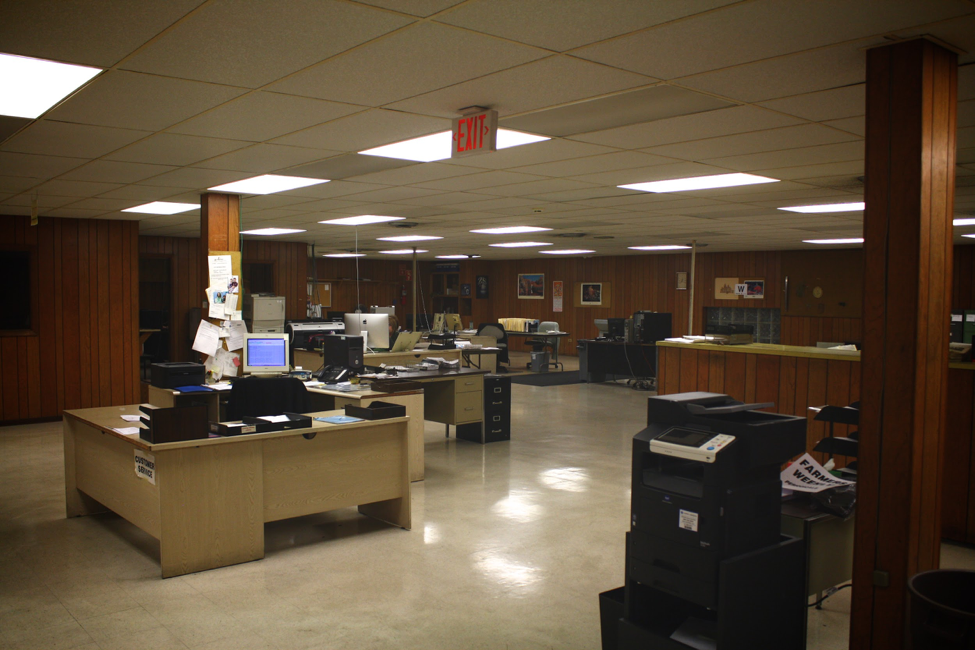
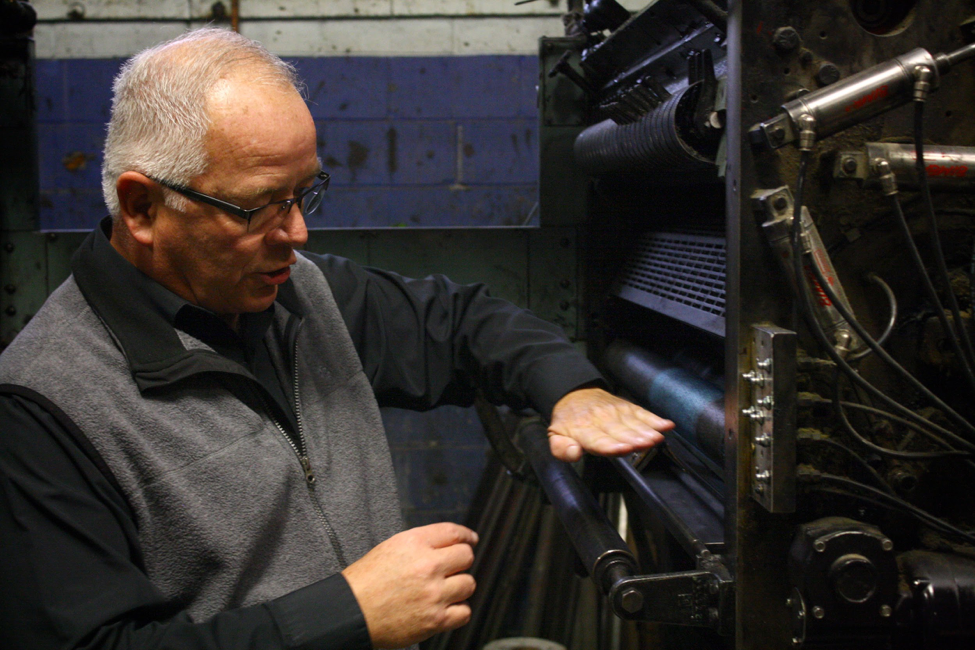
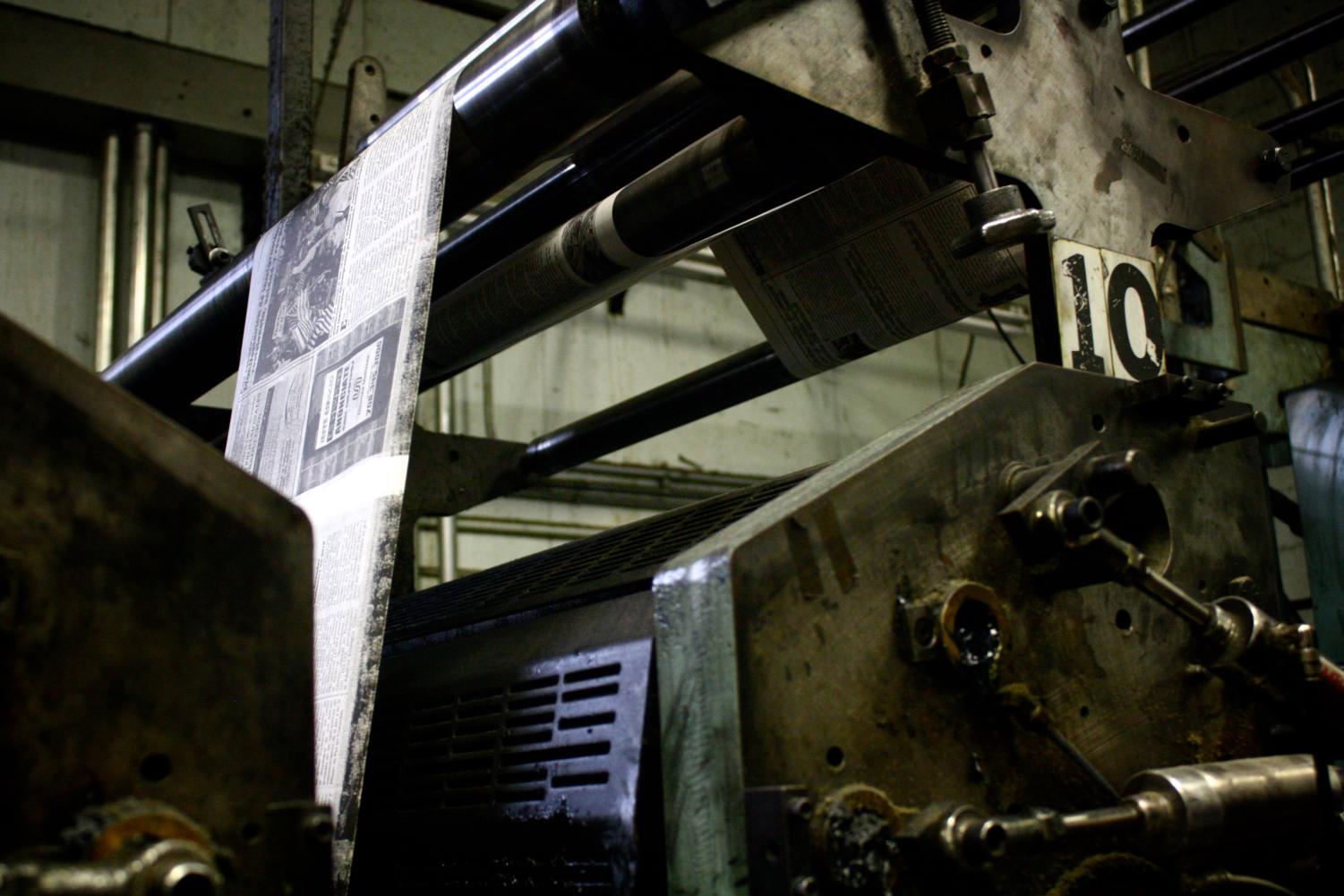

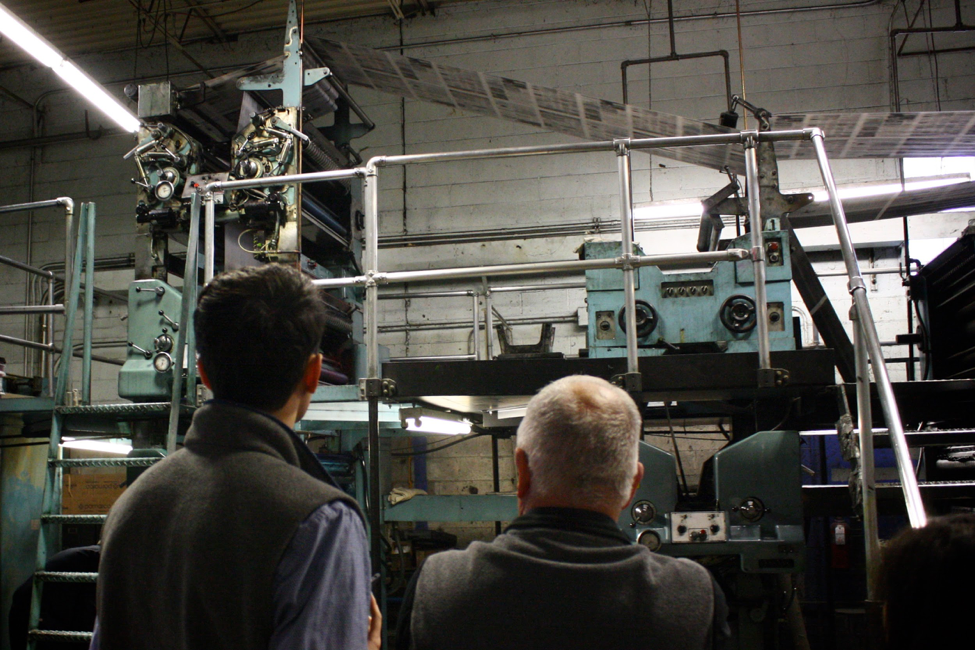
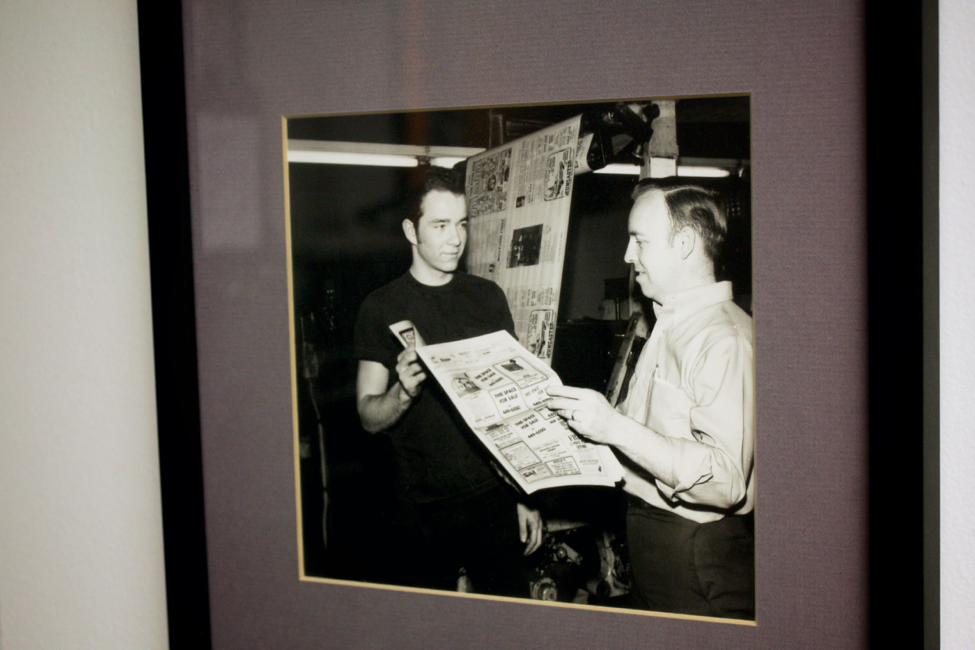